Vegyes flottakarbantartás: A biztonságra törekvés költséges lehet
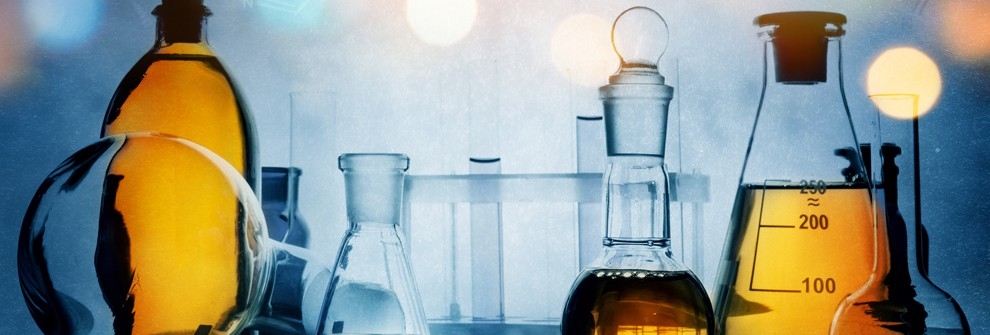
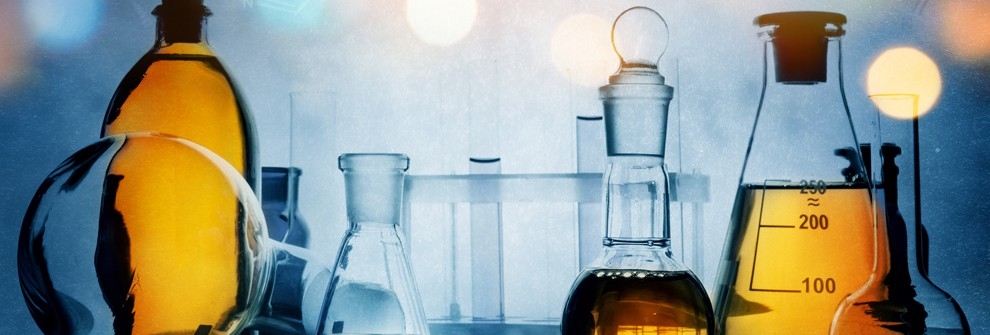
Az építőipari gépek karbantartásával foglalkozó vezetőkkel folytatott beszélgetésekből egyértelmű, hogy a vegyes flották váltak általánossá. A legtöbben a költségkorlátokat és a berendezések minőségének gyártók közötti ingadozását említik, mint fő okot arra, hogy már nem lojálisak egyetlen gyártóval szemben sem.
Bár a vegyes flották csökkenthetik a költségeket és néha javíthatják a teljesítményt, ennek sokszor ára van - és ez legtöbbször a drámaian bonyolultabb karbantartási programban ölt testet. A különböző gyártók eltérő szervizelési és karbantartási intervallumokat, követelményeket és kenőanyagokat írnak el, ami jelentősen bonyolultabbá teszi a karbantartást.
Mit lehet ezzel kezdeni? Sok vezető a hagyományos megközelítés híve a karbantartási ütemtervek és az olajcsere intervallumok terén, és megpróbál egy általános, közös intervallumot találni, amely a flotta egészére működik. Ez azonban legtöbbször a szükségesnél és a gyártó által előírtnál gyakoribb olajcserét és karbantartást jelent. Ez a megközelítés - érvelésük szerint - egy olcsó „biztosítás”, amely véleményük szerint kiküszöböli a rendszeres olajelemzés szükségességét.
Amit ezek a vezetők azonban nem értenek, az az, hogy az olajelemzés nem csak az olajról szól. Az olajelemzés révén sokféle problémát azonosíthatunk a berendezésekkel kapcsolatban - van-e kenőanyag-hígulás, szennyeződés, hűtőfolyadék-szivárgás vagy más olyan probléma, amely ronthatja a teljesítményt? Az olajelemzés segít megjósolni és esetleg elkerülni a váratlan berendezéshibákat.
Ha egy általános karbantartási programok készítünk az egész flottára és elhagyjuk az olajelemzést, akkor megnőhet az anyag- és munkaerőköltség, és akár 11 százalékkal is növekedhet egy adott gép végletes meghibásodásának kockázata.
Nézzünk egy gyakori munkagépet, például egy földnyesőt (scraper). Az olajcserék, ideértve az olaj, a szűrők, a fáradtolaj és a munkaerő költségeit, évente körülbelül 1.540 dollárba kerülnek. Ha feltételezzük, hogy flottája 100 hasonló géppel rendelkezik, és évente négyszer van olajcsere, akkor évente 154.000 dollárt költenek kenőanyagok cseréjére. Rendszeres olajelemzéssel, évente átlagosan legalább egy olajcserét kiküszöbölhetünk gépenként. Más szóval, rendszeres olajelemzés nélkül évente 38.500 dollárral többet költenek a kelleténél. És ez még nem veszi figyelembe az állásidőt, amely lényegesen többe kerülhet, mint az anyagköltség-megtakarítás.
Rendszeres olajelemzés hiányában csökken az általános berendezéshibák előrejelzésének lehetősége is. Például a motorhibák 40 százaléka a hűtőrendszer szennyeződésével kapcsolatos, amelyet egy olajelemzés képes kimutatni. Mennyibe kerül a hűtőfolyadék által károsított motor cseréje vagy újjáépítése? Mondjuk átlagosan 90.000 dollárba. Konzervatív módon, tételezzünk fel egyetlen váratlan motorgenerált évente, 90.000 dollárért. Ezt hozzáadva a 38.500 dollárhoz, az „olcsó biztosítás” már nagyjából 130.000 dollárba kerül évente.
Egy átfogó, megelőző karbantartási program, amely lehetővé teszi, hogy könnyedén nyomon kövesse az összes gyártól előírt csereperiódusát, és ennek megfelelően ütemezze a karbantartásokat - és amely rendszeres olajelemzést is tartalmaz - átlagosan 25 százalékkal csökkentheti a kenőanyag-fogyasztást, és emellett a berendezések magasabb rendelkezésre állását és kihasználtságát is eredményezheti. Minden berendezést a megfelelő, kellő időben tud szervizelni, és a lehetséges hibákat előre tudja jelezni, mielőtt azok bekövetkeznének. Ez nemcsak az anyagköltségeket csökkenti, hanem optimalizálja a termelékenységet és maximalizálja az egyes járművek beruházásainak megtérülését.
A jelenleg alkalmazott karbantartási programja milyen messze van az ideálistól?